The efficiency of photoreactors is of great importance in order to economically implement commercial production. Therefore, photoreactors must be tuned to a particular chemical process. In the past, mostly side-loop photoreactors have been designed and developed for every application involving a complex and expensive procedure requiring an appropriate project duration. Quite often, inefficient photoreactors were used for commercial production due to lack of experience and expertise or because of short project time- lines (time-to-market requirements).
Once the type of photoreactor has been selected (e.g. side-loop reactor), the spectral emission and the radiant power of the lamp, the optical path (annular gap) in which the product is to be irradiated, flux and hydrodynamic behaviour of the solution to be irradiated, heat transfer, and possible gas distribution are the most important process parameters that application specialists must determine to achieve optimal process efficiency.
The high demand for equipment used in scale-up procedures of photochemical processes from laboratory to production scale, motivated Peschl to cooperate with De Dietrich Process Systems, to develop a glass-type photoreactor system of industrial-size, enabling the optimization of a variety of different process parameters.
In addition, the product series was expanded to include metal reactors for photochemical processes under pressure. These systems allow an easy configuration of efficient (side-loop) photoreactors.
Photochemical reactions (homogeneous and (micro) heterogeneous (liquid/liquid and gas/liquid) media) in the temperature range from -20 °C to + 200 °C may be carried out using the latest-generation of side-loop photoreactors. The photoreactors are available with different optical paths and can be used with a variety of standardized options, e.g. in combination with optimized static mixers for gas/liquid and liquid/liquid heterogeneous media reactions, vacuum jacket for insulation and various sensors. All photoreactors are approved for explosion-proof operation. A wide range of light sources in conjunction with electronic ballasts, safety-rated control and monitoring equipment completes the portfolio.
This series of photochemical reactors enables all users for the first time to configure and optimize photoreactors for an industrial scale in the shortest possible time. The modular system, may be – at any time – easily adapted to changing process conditions. Different photochemical processes can be developed whit minimized scale-up risks.

With Peschls MPDS®BASIC system, the Modular Photochemical Development System (MPDS®), fundamental feasibility studies are performed in the laboratory.

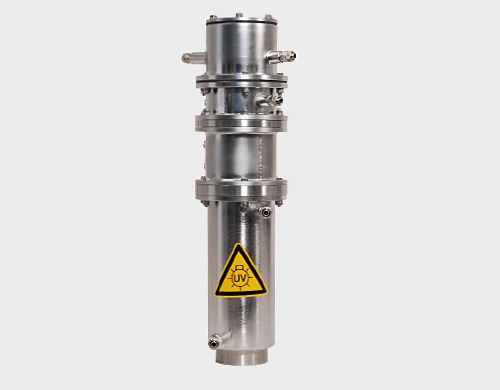
Pilot photoreactor systems are available to guarantee a safe up-scaling process in complex synthesis steps, with the aim to quantify the space-time yield and productivity of the industrial-sized photoreactor. With this data, more precise CAPEX and OPEX analysis can be performed and hydrodynamic effects can be analysed and understood.

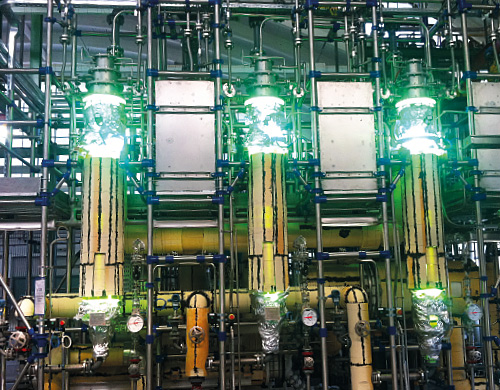
Industrial-size photoreactors are commercially available and tailor-made for each individual process. However, based on the high level of standardized components, such as immersion lamps with Ex-approvals, this task is routine and can be performed fast and reliable with the power density required for highly efficient production.
Typical Processes with side-loop photoreactors
- Vitamins (e.g. pre-Vitamin D2 or D3 and derivatives by electrocyclic reaction or Vitamin A by cis-trans isomerization)
- Active pharmaceutical intermediates (API), e.g. synthesis of Artemisinin (antimalarial drug), singlet oxygen reaction
- Fragrances (e.g. singlet oxygen reaction: Rose oxide
- Plant treatment intermediates (e.g. pinacols by photo-hydrodimerisation)
- Lubricants (e.g. Fomblin)
- Intermediates for diagnostics (e.g. by photo- bromination or photo-iodination)
- Chlorinated solvents (e.g. dichloromethane, chloroform, tetrachloromethane)
- Chlorinated intermediates for synthesis (e.g. benzylchloride, benzalchloride, methylchloride)
- Brominated intermediates for synthesis (e.g. substituted benzylbromides)
- Polymer and co-polymer specialities (photopolymerization in homogeneous (liquid), heterogeneous (liquid/liquid and liquid/gas (aerosols) media)
- Polymer functionalization (e.g. synthesis of API carriers, photo-halogenations, photooxidations in solid/liquid or sold/gas microheterogeneous media)
- Safety agents (e.g. odour additives for gases)
- Fluorinations, Sulfoxidations, Nitrosylations
Technical Features
- Modulized toolbox system, fast to be configured
- High molecule exchange on the barrier surface
- Optimized residence time in the irradiated reactor volume
- Optimized gas injection and distribution due to special gassing systems
- Maximum pumping rates through the irradiated zones of the reactor
- Laminar and turbulent operation
- Ex-proof design of all components
- Up to 60 kW lamp power
- Gas-discharge, Excimer and LED lamps
- High cooling efficiency through the vessel wall or internal heat exchanger
- Hydrodynamic optimization by flow simulations (CFD)
- Process temperatures from -25°C up to 200°C
- Robust and reliable reactor designs for safe production
- Special materials of construction such as titanium, ceramics or special glass-lining for aggressive process conditions
Services we offer
- Engineering and supply of industrial-sized photochemical reactors
- Scale-up of your process from lab-size to industrial-size
- Scale-down of your process from industrial-size to mini-plant-size
- Photochemical process consultancy
- HAZOP studies for safe operation
- Commissioning support, on-site service
Any questions?
Please ask us