The integration of immersion lamps into agitated photoreactors to perform photochemical reactions may present a high risk of breakage, and such type photochemical reactors has mostly been ruled out in the past. The risk of breakage is not only due to the lateral forces originating from stirring and acting on the glass components of the immersed lamps, but also to frequencies and resonances that arise during operation and represent an additional mechanical load. Therefore, it is not recommended to carry out photochemical processes in agitated photoreactors without well-founded data, detailed mechanistic understanding, FEA (Finite Element Analysis) and simulation and validation of the mechanical effects in industry-sized vessels.
Peschl Ultraviolet, a leading developer and manufacturer of UV systems for applied photochemistry, has entered into a cooperation with EKATO, a leading designer and manufacturer of special material agitators and reactors, to take on this complex task. In cooperation with EKATO, we have succeeded in developing and manufacturing safe agitated photoreactors for which process guarantee can be provided and mechanical integrity can be guaranteed.
To ensure the mechanical integrity of the immersed lamps, extensive stress and fatigue analyzes, stiffness and deflection analyzes as well as modal/vibration analyses have been carried out. In extensive series of tests, the mechanical stability of glass tubes and their load limits have been analyzed. Hydrostatic pressure tests and measurements under real conditions on an industrial scale were used to validate the theoretical calculations in practice.
With this cooperation between the experts of Peschl Ultraviolet and EKATO, stirred-tank reactors – still the “workhorse” of the chemical industry – have now been adapted to the requirements of photochemical processes. Safe, efficient and reliable stirred photo-reactors of industrial size are now commercially available. Beside these production sized photoreactors, a range of laboratory- and pilot photo-reactors has been developed as part of this cooperation, allowing the development of photochemical processes in stirred reactors from laboratory to industry-size with comprehensive process guarantee.
Rely on the Peschl/EKATO team to execute your project from laboratory- to industrial plant-scale in shortest lead times from a single source.

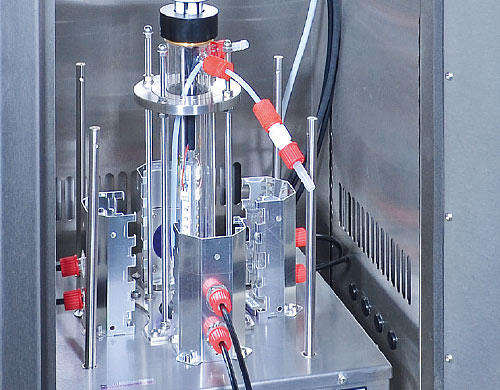
Our Modular Photochemical Development Systems (MPDS®) is used in the laboratory. With the MPDS®BASIC system, fundamental feasibility studies are performed.

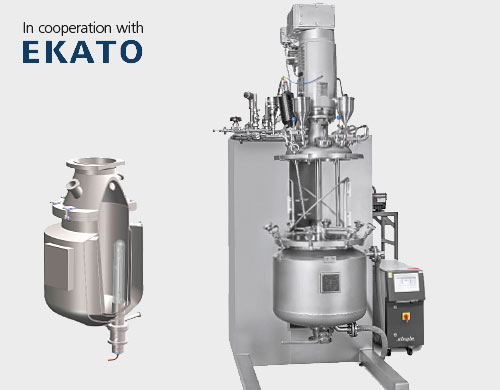
Pilot photoreactor systems are available to guarantee a safe up-scaling process in complex synthesis steps, with the aim to quantify the space-time yield and productivity of the industrial-sized photoreactor. With this data, more precise CAPEX and OPEX analysis can be performed and hydrodynamic effects can be analysed and understood.

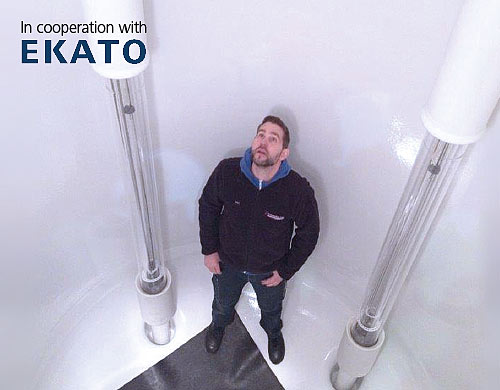
Industrial-size photoreactors are commercially available and tailor-made for each individual process. However, based on the high level of standardized components, such as immersion lamps with Ex-approvals, this task is routine and can be performed fast and reliable with the power density required for highly efficient production.
Typical Processes
- Material modifications (processes in heterogeneous – liquid/liquid and solid/liquid – media (e.g. chlorinated rubbers, chlorinated PVC (C-PVC))
- API carriers and particle modifications (processes in heterogeneous (solid/liquid) media)
- Sulfoxidations and sulfochlorinations (e.g. Sulphochlorinate polyethylene)
- Photocatalyzed and photo-redox processes (processes in heterogeneous – solid/liquid – media)
- Photopolymerizations (radical and cationic) in heterogeneous – liquid/liquid and solid/liquid – media) (e.g. Caprolactam as pre-cursor of Nylon 6, Lauryllactam as pre-cursor of Nylon 12, Polyacrylates, Polystyrenes and co-polymers, mini-emulsions with monomer functionalization)
- Photohalogenations
- Nitrosylations
Technical Features
- Optimized residence time in the irradiated reactor volume
- High circulation rates of particles and slurries to the light source
- Optimized gas dispersion and gas-liquid mass transfer due to special gassing systems
- Solids homogeneously suspended due to high-performance impellers
- Maximum pumping rates through the irradiated zones of the reactor
- High cooling efficiency through the vessel wall or internal heat exchanger
- Hydraulic loads on UV-lamp system are determined by flow simulations (CFD) and measurements in full scale
- Optimized and validated before manufacturing by CFD studies
- Elimination of scaling inside the reactor by high velocity
- Reactor size up to 50 m³
- Hermetic sealing to the atmosphere in the unexpected event of broken glass tubes
- Ex-proof design of all components
- Power consumption up to 60 kW per UV-Lamp
- Gas-discharge, Excimer and LED lamps
- Process temperatures from -25°C up to 200°C
- Process pressure rating from -1 to 100 bar
- Robust and reliable reactor designs for safe production
- Special materials of construction such as titanium, ceramics or special glass-lining for aggressive process conditions
Peschl Ultraviolet cooperates with EKATO in the domain of agitated photoreactors.
Services we offer
- Engineering and supply of industrial-sized photochemical reactors
- Scale-up of your process from lab-size to industrial-size
- Scale-down of your process from industrial-size to mini-plant-size
- Photochemical process consultancy
- HAZOP studies for safe operation
- Commissioning support, on-site service
Any questions?
Please ask us