For decades, special medium-pressure gas-discharge light sources have been the standard technology used in photoreactors to carry out photochemical reactions. While gas-discharge lamps often have an efficiency of just 5-7% depending on the wavelength, LED light sources offer up to 60% efficiency with high selectivity. However, some obvious technical problems had to be solved, prior LED technology could be introduced in commercial scale photoreactors, so Peschl started a development program back in 2017 and finally invented a special proprietary LED technology.
With the inventions made, Peschl was able to eliminate lifetime problems due to volatile organic compounds (VOCs), eliminated near field reflexion issues, increased the photonic output and realized the required thermal de-coupling. Today Peschl offers a wide range of robust and reliable industrial scale LED Photoreactors which have been qualified successfully under harsh industrial conditions. All commercial scale LED photoreactors are available as flameproofversions with dimming and safe shutdown technology.
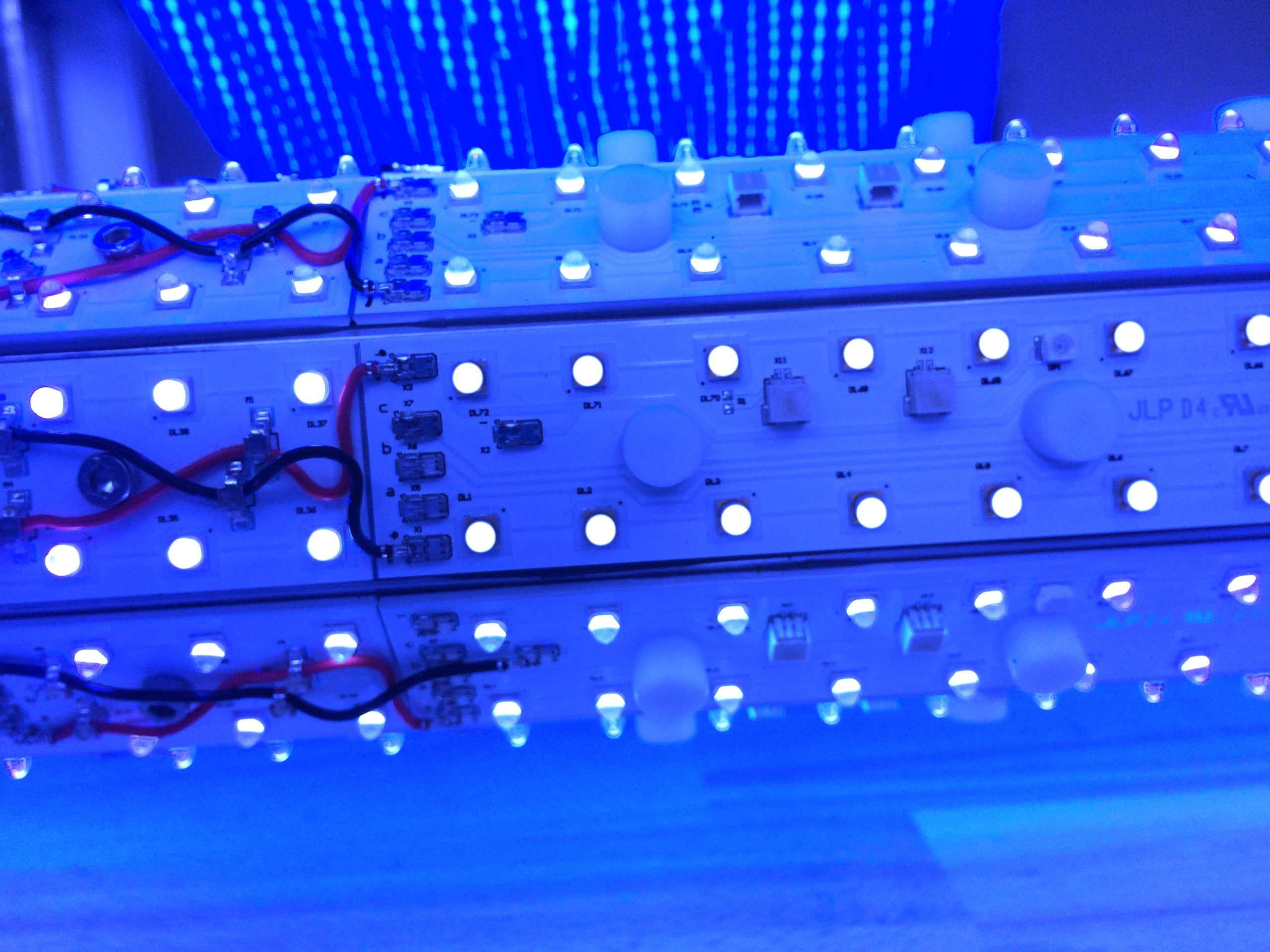
Innovative LED-Technology
Peschl developed an innovative LED technology where the LEDs are submerged into a non-conductive, highly transparent, chemically inert thermofluid called “trisco®UV”, which has the same refraction index as the immersion tube made of glass. The design has been engineered in a way that a very homogeneous light pattern is generated to prevent dark zones and hot spots. LED-Photoreactors are available with up to 5 kW power consumption per LED lamp, which is an equivalent to 30 kW medium pressure lamps. Available wavelengths are between 365 nm and 625 nm with efficiencies of up to 60%.
Assembly of the LED-Photoreactor
The immersion lamp system consists of a pressure-tested stainless steel head section which can be completely removed from the base flange for assembly and maintenance purposes.
Inside the head section is the electrical connection area. This electrical connection area is inerted via nitrogen via leakage compensation mode. The base flange defines the interface to the photoreactor and is available in different materials of construction such as Stainless steel, Nickel alloy, Hastelloy or Titanium as well as with PFA lined stainless steel.
The base flange accommodates the quartz-glass immersion tube with a special flange system, which is mounted in such a way that the seal is permanently guaranteed in industrial applications – even with high temperature fluctuations. This is ensured by a special sealing system and patented flange connections.
The immersion tube is thus flexibly mounted, and the sealing task is technically decoupled from the mechanical force transmission, so that tensile stresses cannot occur in the glass tube. The mechanical fixation is part of the reactor design.
Inside the immersion tube is the oil-encapsulated LED radiation source with longitudinally watertight cable bushings as well as the supply and return system of the thermoliquid. A special sealing ensures that the encapsulation is permanently maintained and remains tight.
Each LED-Photoreactor comes with a dedicated power- and control cabinet and a media panel for safe operation and DCS connectivity.
Any questions?
Please ask us